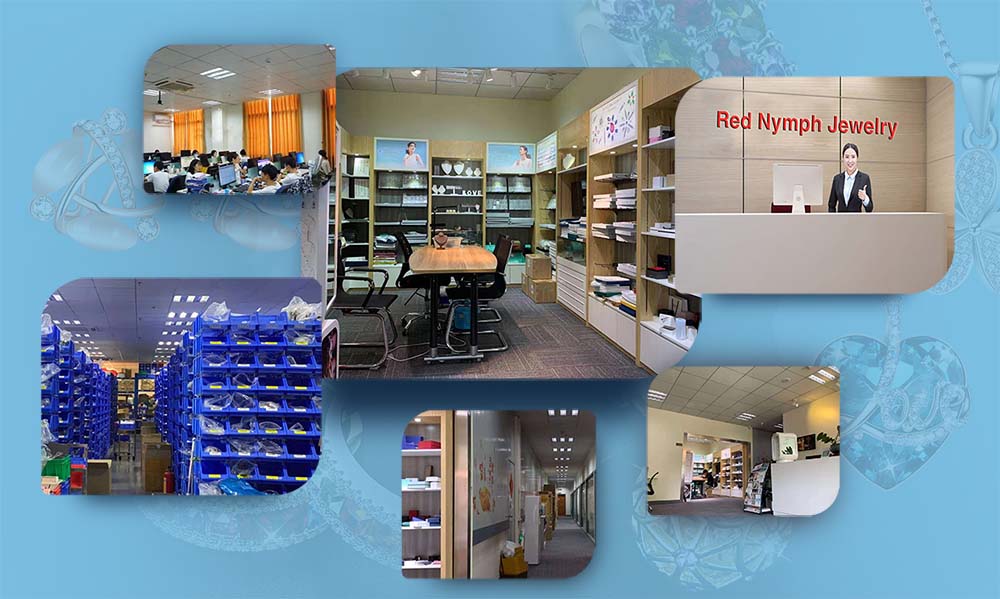
Red Nymph Jewelry
Something remarkable happened to jewelry design and manufacturing in the past few years – it underwent a technological revolution powered by Computer-Aided Design (CAD) software and Computer-Aided Manufacturing (CAM) hardware, such as 3D printers.
Before these technological advances, designers began by sketching a piece of jewelry, and when it was finalized, they used pencil, pen, or watercolor paint to create a rendering of the design . Jewelers then used the drawing to either hand-fabricate the piece out of metal or carve it out of wax. The wax model was encased in plaster and placed in an oven. Once the wax was burned away, molten precious metal, like gold or platinum, was poured into the cavity left by the wax . After it cooled, the plaster was broken apart and the piece of jewelry was finished.
Designers still use many of the steps in this process, especially when making high-end pieces. And despite all the new CAD and CAM technology, jewelry designers still need to have good engineering skills – like knowing how strong prongs have to be to hold a gemstone in place .
Still, technology has fundamentally changed how jewelry is designed and manufactured.
Computer-Aided Design
Much of today’s jewelry is now designed using CAD software. The allure is understandable: CAD allows designers to work more quickly, easily create variations of a design theme, and “cut and paste” motifs into different projects more quickly than if drawn by hand. Designers can also save favorite functional or decorative elements in a library and use them in future pieces.
The more complex a piece of jewelry is, the more difficult it is to design . Another way that CAD software is changing design is that it allows designers to zoom in so they can add detail to very small areas of a piece.
CAD also helps the creative process. A good design is usually the result of considerable experimentation. CAD makes trial and error easy (you can’t quickly “undo” something you don’t like in a watercolor). Designers can follow their imagination without having to recreate the design each time they are inspired.
CAD also lets designers create photorealistic images of jewelry that have shadows and reflections. These computer-generated images are so lifelike they can even fool an expert’s eyes. These images let consumers and creative directors get a good sense of what a finished piece will look like before it is made.
Computer-Aided Manufacturing and 3D Printers
In the past, manufacturers used rubber molds to make duplicates of the original master model. However, if variations on that model were needed, the model maker would have to create a whole new model. With CAD software, changes can made with clicks of a mouse, and the new model can be printed on demand on a CAM machine, such as a 3D printer. 3D printers enable manufacturers to print resin prototypes of the CAD model that can be easily cast.
Laser Sintering
Laser sintering promises to be the next big thing to revolutionize jewelry manufacturing. A laser melts powdered metal, like gold, platinum, or silver, layer by layer into the shape of a piece. Pieces with working hinges and pins can be made – no small feat. The technology is still quite expensive and in its infancy, but it may eliminate the need to create a wax or plastic model of a piece and then cast it. In other words, a designer could go from a CAD model to a finished piece with just a few mouse clicks.
Looking Back to Look Ahead
Ten years ago, the notion of designing a piece of jewelry on a computer seemed farfetched to some. Ten years from now, designers may create a piece in CAD, send it to a laser sintering machine, and hold a near-completed work in their hands. What’s more, each piece could be customized to the consumer’s specifications. It’s definitely an exciting time to be a designer and a jewelry connoisseur.
Leave A Comment