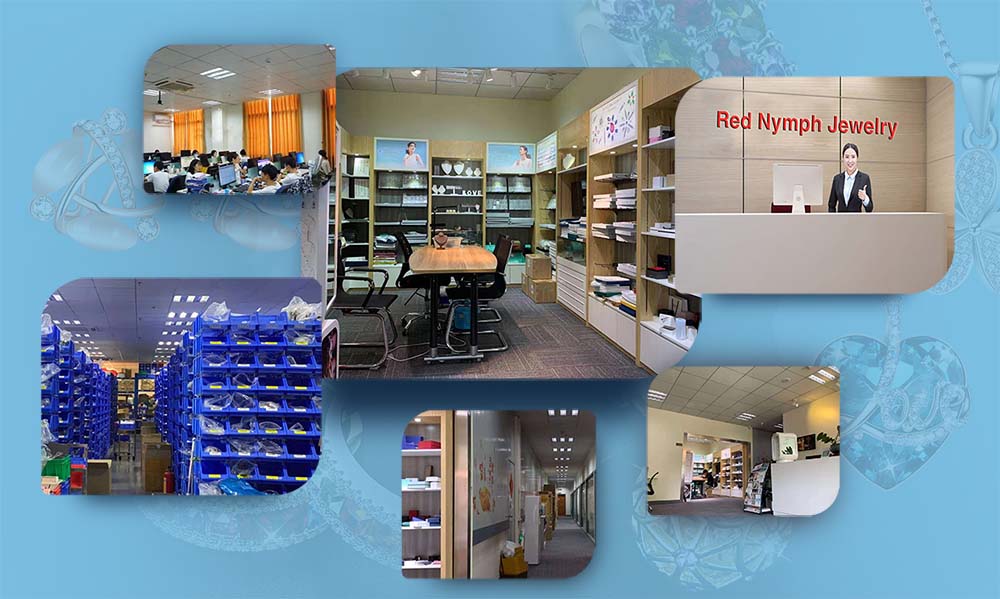
Red Nymph Jewelry
Silver jewelries are welcomed by more and more consumers because silver materials are easier to obtain, the price is not very expensive, and a variety of fashionable styles can be easily made, actually, Making sterling silver jewelry is a hobby for some and a business for others. Silver clay is a great way to get started if you can get hold of it, but you can also cut, attach, or mold solid sterling silver with a jeweler’s saw, soldering kit, or hammer and anvil. Combine several techniques for innovative results.
1) Select a heat source. After sculpting the clay, you’ll need to fire it at high heat in order to burn away the the binding material and leave only the silver behind. Some brands of metal clay can be fired over a gas stove, while others require a gas torch or even a kiln. Check what temperatures you can achieve with your tools before you select a clay.
You’ll need a stainless steel mesh if using a stove.
Find a heat brick if using a gas torch.
A kiln is recommended for large or thick items.
To estimate the temperature you can achieve on your gas stove, heat a small, thin aluminum pan on high and point an infrared thermometer at the surface once it is fully heated.
2) Purchase sterling silver clay. You may need to order this online, as not many art stores have it in stock. Pure silver clay is significantly more common, but the resulting jewelry will be less sturdy.
You can purchase this in lump form for sculpting, as a softer paste extruded from a syringe for finer detail work, or even in “paper” form for origami designs.
3) Form the clay into the design of your choice. You can sculpt this clay with hands or ordinary sculpting tools, add detail with a knife or wire, or cut it into shapes with stencils.
The silver clay will shrink during firing, so make the jewelry slightly on the large side. Check the label for details, as shrinking can vary from 8% to 30% between products.
You can push a metal stamp or any metal object into the clay to form a surface design.
4) Dry and sand the clay. Allow the silver clay to air dry overnight, or dry it thoroughly using a hairdryer. Smooth the surface with fine sandpaper.
5) Fire the clay with a torch. If using a torch, place the clay on a heat brick, and the brick on a heat-safe surface. Hold the torch flame ¾ inch (2 cm) from the clay and heat until it catches fire, burns out, glows red, then reaches an even glow. Continue to heat for at least five minutes, or however long your clay instructions recommend.
6) Fire the clay with a gas stove. If you are using a gas stove, follow these instructions instead:
Place a piece of stainless steel mesh on a stove top burner. Turn the burner on to its highest setting.
Observe the mesh to locate the hottest area on it. This area will glow. Turn the burner off and allow the mesh to return to it’s normal color.
Place the silver onto the hottest area of the mesh and turn the burner back on, this time to a low flame. Use tweezers or flat, non-serrated pliers to handle the silver.
After the clay has burned off completely, turn up the burner and heat until the silver glows red. Turn it down again if it glows orange.
Continue heating for ten minutes, then turn off the heat.
7) Fire the clay in a kiln. If you have a kiln, you’ll be able to follow the precise recommendations on your silver clay. Maximum strength may be achieved with a long firing at relatively high temperatures, but there may be a faster firing option outlined on the instructions as well. A specialized jeweler’s kiln will fire faster, but a ceramics kiln will work as well.
The optimal firing temperature for most silver clay is 1650ºF (900ºC), held for 2 hours, but the jewelry might come out strong enough even at temperatures as low as 1200ºF (650ºC).
8) Quench the silver (optional). Letting the silver cool on its own is recommended. If you are in a rush, you can quench the hot silver in cool water to bring it down in temperature, although it may still not be safe to touch for a few minutes. This can cause structural issues if reheated for adjustment later, but thorough drying can prevent this.[6]
Never quench jewelry with embedded glass, precious stones, or other additions.
9) Polish the surface (optional). The silver will look white and a little dull after firing. If you want the shiny silver appearance you may be used to, brush the surface with a brass or steel wire brush, or polish with a buffing machine and jeweler’s rouge.
After reading this article, do you know something about the making of silver jewelries? Interested people are also welcome to contact red nymph to discuss more
Leave A Comment